Integrated Impedance Spectroscopy for Automated High Throughput MR Measurements on Fluidic Plugs
Seminar Abstract
Omar Nassar, Mazin Jouda, Nan Wang, Michael Rapp, Jan Korvink, Dario Mager, and Neil MacKinnon
Institute of Microstructure Technology, Karlsruhe Institute of Technology (KIT), Germany
Microfluidic technologies combined with micro-NMR have become increasingly popular given their promise of increased sample throughput and mass-sensitivity. A common challenge is the relatively large dead volume in the tubing feeding the micro-NMR detector. To circumvent this issue, concentrated sample plugs may be dispersed within an immiscible fluid. This two-phase flow eliminates the dead volume, but requires continuous online measurement to track the plug positions and ensure that the desired sample completely fills the NMR detection volume. In this contribution, a flow system featuring i) integrated impedance spectroscopy sensors for sample position and flow rate measurement, and ii) a micro saddle coil for NMR spectroscopy is demonstrated. By loading a tube with several samples separated by an immiscible fluid, this flow system enables fully automated NMR spectroscopy while simultaneously taking advantage of the improved experimental time per sample due to continuous sample flow.
Interdigitated electrode (IDE) sensors and a micro saddle coil were fabricated on a Kapton foil using an established process (Wang, N., et al., J Micromech Microeng 28 (2018) 025003). A 25 μm Kapton foil laminated on one side with a 9 μm copper layer was used, which was structured using photolithography. An insert was built (Fig. 1) by rolling the structured Kapton foil around a 2 mm glass tube with a 1.6 inner channel. The two IDE sensors were positioned 1 cm before and after the saddle coil to enable flow sensing in both directions and flow rate measurement, permitting real-time calculation of the appropriate delay before triggering NMR acquisition. Each IDE sensor covered a length of 5 mm and the saddle coil had a detection region of 5 mm. A Teflon tube carried the samples and fit inside the glass capillary to avoid fluidic junctions and ensure smooth sample flow. The inlet and outlet of the tubing were connected to a syringe pump and flow was controlled from outside of the magnet. A Zurich Instruments UHFLI amplifier was used to drive the IDE sensors (frequency = 540 MHz) and measure the impedance to sense the position and the speed of the water plug and trigger NMR acquisition. NMR spectra were acquired at a 1H Larmor frequency of 500 MHz using a Bruker AVANCE III spectrometer.
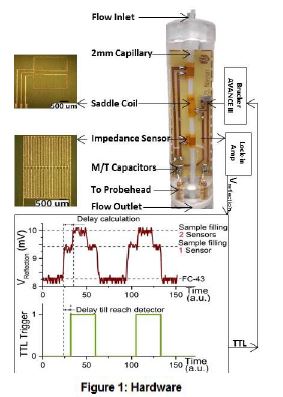
Two experiments were performed. In the first experiment , the tube was filled with a single aqueous plug (20 cm long) bordered by FC-43, and the flow was controlled by the syringe pump at a flow rate of 1.0 cm / s running continuously until the aqueous plug left the NMR probe. NMR acquisition was done with and without the triggering system. In the second experiment, the tube was filled with nine different 5 cm aqueous plugs each separated by 10 cm of FC-43. The first plug was used as a dummy sample to calculate the trigger delay and the flow was running continuously until all the sample plugs left the NMR probe.
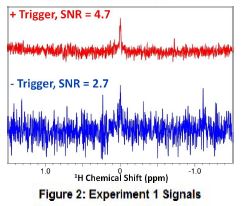
Impedance measurements could robustly distinguish the water and oil phases. Importantly, driving the electrodes had no visible deleterious effect on the 1 H NMR spectrum. It was observed that the SNR was improved by 75% when implementing the automated triggered data acquisition (Fig. 2), even with a relatively long sample plug. Micro-coil integration with impedance-based sensing of flow has been demonstrated. With this technology we believe high-throughput, automated sample measurement (Fig. 3) will be possible in a dual-phase, droplet-based approach where each droplet could be a different sample, thereby reducing the required sample volume significantly.
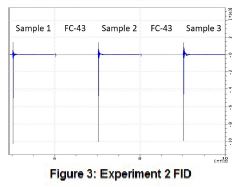